Le coût de production, c’est l’obsession des ingénieurs qui construisent la nouvelle fusée. Celle-ci leur a été imposée par un changement radical et rapide du marché des lancements de satellites : l’arrivée de la société privée américaine Space X qui, avec sa fusée Falcon 9, a littéralement cassé les prix. De plus,...
Robotique, impression 3D : comment Ariane 6 se construit plus vite et moins cher
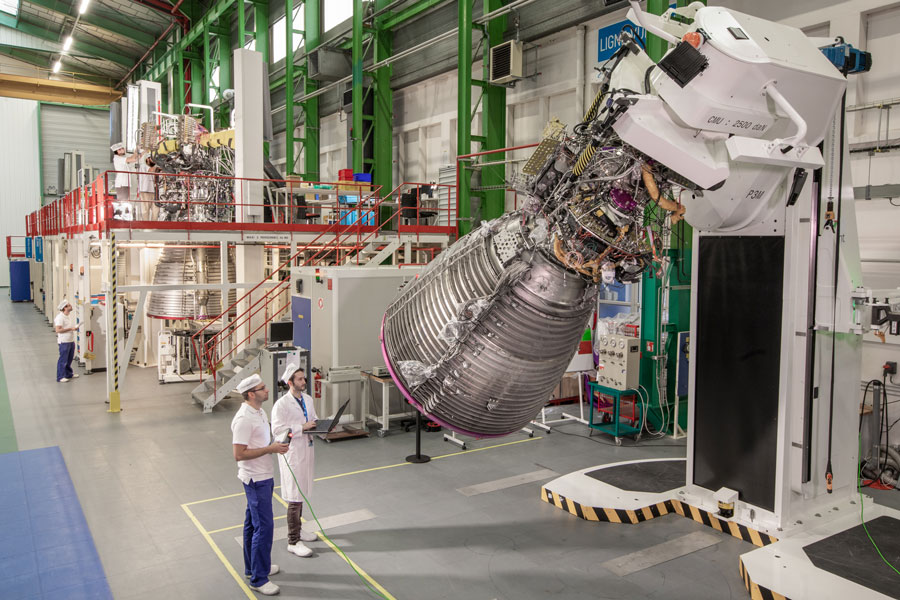
Le coût de production, c’est l’obsession des ingénieurs qui construisent la nouvelle fusée. Celle-ci leur a été imposée par un changement radical et rapide du marché des lancements de satellites : l’arrivée de la société privée américaine Space X qui, avec sa fusée Falcon 9, a littéralement cassé les prix. De plus,...